The seed is found on the top of a flowering tobacco plant and planted.
Seedlings are grown and selected based on good-looks and taken to the fields to grow.
Plants mature. Leaves grow. Life is good. Leaves are then picked from top to bottom of the tobacco plant.
Weather, soil, and myriad of other factors play into a healthy tobacco plant. Skilled workers inspect and care for the plant each day during their growth.
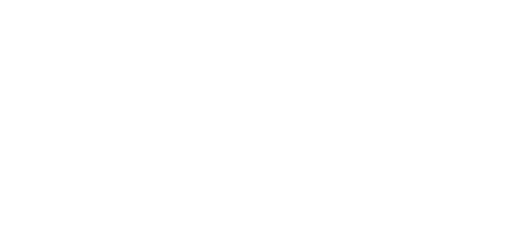
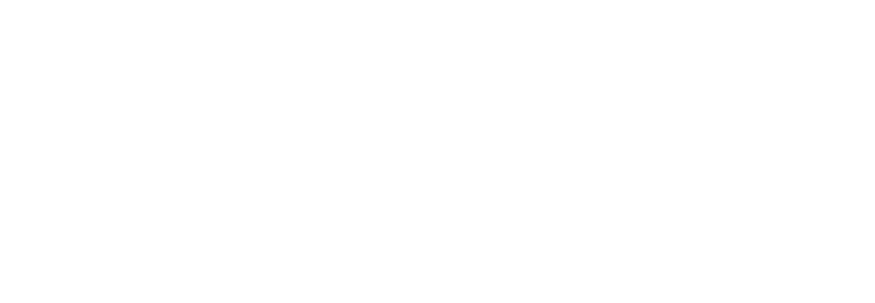
Leaves are pulled by hand. They are moved to the curing barn. Like drying flowers, they hang upside down changing color from bright green to brown.
Cured tobacco is pulled from the barn and moved to a fermentation space. Thousands of leaves are stacked up in pilons. Moisture and pressure work together to “break down” the leaves and remove impurities. Walk into one of these rooms without a mask and you’re likely to pass out from the ammonia being worked out of the tobacco.
Incredible attention is paid to leaves during the fermentation process. Temperature is tracked daily. Pilons are rotated. One small error could result in hundreds of thousands of dollars in unusable tobacco.
Your tobacco is anywhere from 2-5 years old now. Fermentation has played its part and the tobacco flavor is coming to life. Smaller bales of tobacco will rest/age until they are ready to be rolled on the production floor.

There are 3 important parts of a cigar that make its blend. Filler, binder and wrapper. A Master Blender considers flavor, strength, aroma, combustibility, appearance, and smoke production before forming the cigar. Even then, leaves age. Flavor may change over time, tasting great today but what about in a year, or two?
Numbers are important in blending. Some leaves are rare and can only be used for small quality limited edition cigars.
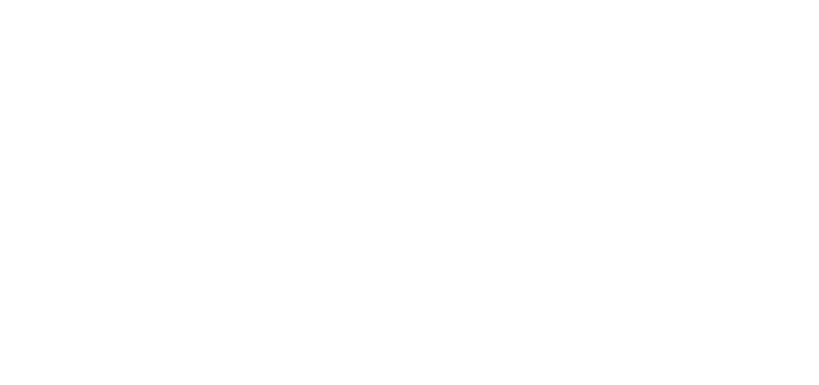
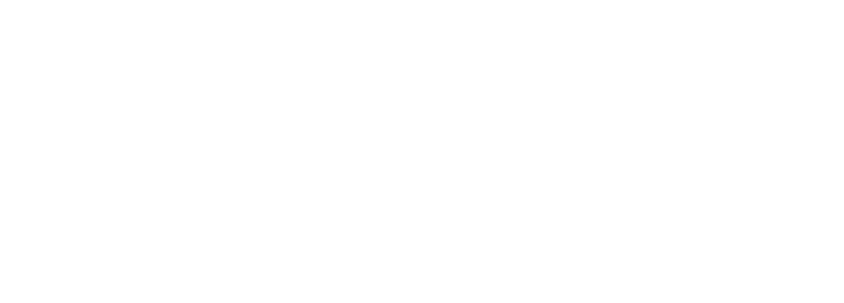
Enter rolling team. Usually two craftsmen, the first, the bunchero (buncher), is responsible for putting the blend of filler leaves together and rolling them into a binder (a single leaf that holds the cigar together). Once the bunchero finishes his part of the process, the filler/binder is placed into a mold where it will secure the cigar shape before the roller takes over.
The second craftsmen, a roller, is responsible for wrapping the cigar with the leaf you see and know as the cigar wrapper. Then, a small piece of tobacco is cut from the leaf and placed on the end of a cigar like a cap. The cigar is carefully checked for hard/soft spots and is then placed in a pile where it will undergo further inspection. Once approved by a supervisor, the cigars will be placed in bundles (half-wheels) where they are aged.
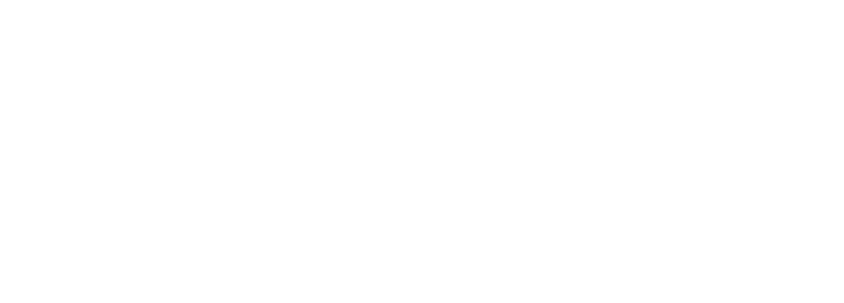
Blended to perfection the cigars are placed in an aging room for 3 more weeks or even several years more.
After aging, cigars are spread out over a table. Because leaves vary in color they are separated and sorted by similar colors for the best possible match.
They are handed off to the packing team. Here, factory workers place the cigar band on each cigar by hand. If the cigar is packed in cellophane, the worker carefully places the cigar in the wrapper. All cigars are placed in their proper box an sealed.
You make a visit to your favorite cigar shop in the East End of Pittsburgh. The folks at Dirty Dog are thrilled to see your beautiful half shaven face.
You open a box of your favorite cigars. Lighter ignites. Smoke ensues.
That is the story of a cigar: from seed to smoke.
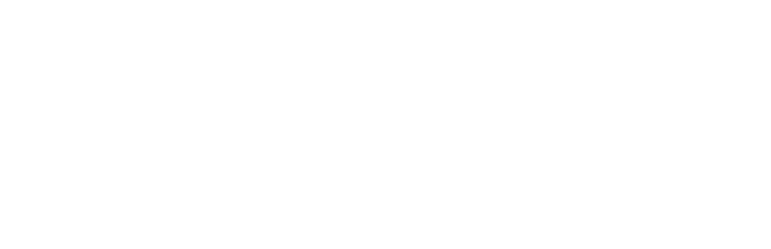